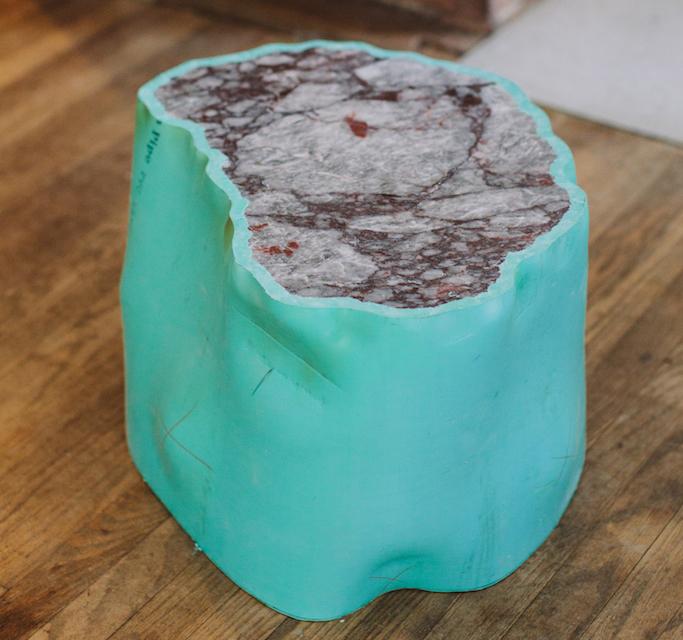
06.20.13
Sighted
Jack Craig on L’ArcoBaleno
In some ways, L’ArcoBaleno — the new design buying site from Ambra Medda, former founding director of Design Miami — isn’t so different from our own home here on the web. Both sites mix a curated marketplace with original editorial content; both emphasize process and context, and champion emerging talent. But of course here at Sight Unseen, we limit our shop selections to things that can be shipped USPS in a Priority Flat-Rate box. On L’ArcoBaleno, which launched earlier this week, one can purchase — with insured shipping of course — collectible designs from around the globe, ranging from a $23,000 blown-glass totem by newly christened design darling Bethan Laura Wood to a $75,000 Plexiglas and car lacquer dining table by Maria Pergay. The site is bit like a more avant-garde 1stdibs; it’s also a lot like the Design Miami fair itself, if you could make impulse purchases in the Aranda/Lasch pavilion at three in the morning.
But even if you’re not flush enough to be a customer, there’s still reason to visit L’ArcoBaleno beyond lustful Pinterest-ing. The Features section mixes fascinating object lessons (a history of, say, Shiro Kuramata’s Nara Table) with Q&As and “making of” stories, and it was the latter that caught our attention while we were browsing the site earlier this week. We’ve long been obsessed with Detroit designer Jack Craig’s Pressed Tables; when we saw them in person at Johnson Trading Gallery a few weeks back, we found ourselves wondering precisely how they were made. Was the stone merely a slab top, or was it a huge hunk encased in PVC? How heavy was it? (Paul Johnson graciously offered to let us pick it up; the answer — not very!)
The piece we’re excerpting today from L’ArcoBaleno tells the story of this very product, and gives insight into Craig himself (apparently a former Navy engineer!) Read the story here, then visit L’ArcoBaleno for lots more like it.
Text by Anna Carnick
Photography by Michelle and Chris Gerard
At first glance, Jack Craig’s Pressed Table appears almost otherworldly. It is a charming but curious combination of stone fragments encased in a futuristic, turquoise shell. Sleek and even a bit archeological on top, at its bottom, seemingly haphazard curves jut out from its core, giving the impression that something or someone is trying to get out.
Dig a little deeper, though, and one realizes that this ambiguous outer layer is, in fact, repurposed PVC water main piping. And Pressed is the latest addition to Craig’s ongoing PVC Series—an experimentally driven collection that has allowed the Detroit-based designer to push the material to its physical limits. Embracing readily available resources, PVC combines craft, design, and industry to play with observers’ preconceived notions of common objects. As Craig says, “The ordinary can be activated, amplifying everyday experiences.”
“I like setting up experiments where the results are indeterminate,” he notes. He has spent the past year doing just that, heating and manipulating PVC by hand—stretching, folding, and pressing to test its boundaries. Once the plastic is molten, he inserts contrasting, natural materials. Previously, these included locally sourced wood and steel; most recently, with Pressed, he incorporates stone fragments salvaged from granite and marble countertop fabrication shops around the city.
“I learn by experimenting,” he says. “I do dozens of material studies and models, all based on simple, one-man, low-tech techniques and how they can transform.”
Depending on size, each Pressed Table takes anywhere from a few days to a few weeks to complete. To begin, Craig—a former engineer for the U.S. Navy’s infrared division and a 2012 graduate of Michigan’s Cranbrook Academy of Art—procures a 20-foot-long, 2-foot diameter, 600-pound PVC tube from a local industrial plumbing distributor called Etna Supply. (Surprisingly, these pressure-resistant tubes come in white and pastels, each hue signifying a different industrial purpose.) Craig cuts the pipe down to size—a ballpark 22 inches long per table—with a handsaw in the parking lot outside his studio.
“Few get to see that much plastic at once,” the designer acknowledges. “Confronted with these volumes, there is a kind of reduction. You experience them for their sheer materiality. It is completely foreign, but the strangeness sets up opportunity.
Once the PVC is cut, Craig heats up the individual pieces, holding a propane space heater in one arm and rotating the pipe in the other, until the PVC reaches a malleable, molten effect. “I look like some sort of World War II-era flame-thrower soldier,” he laughs
Each cut piece of plastic weighs between 30 and 50 pounds on its own. “That’s part of my fascination with them,” he says. “Ultimately, they are plastic, and the tendency is to think of that as a cheap material. But at this size and weight, it plays with your ideas of value.”
When the piping is heated and pliable, Craig has a five-minute window in which to act, before the plastic cools. He uses a quick, simple gesture to place the stone fragments inside. When the PVC loses heat, it condenses around the inner material, defining the table’s ultimate form—a process Craig refers to as “fossilizing.”
With Pressed, this particular step has developed even further. As he explains, “Instead of a single applied force, the latest forms are derived from a series of applied pressures. The plastic is stretched and compressed in multiple directions; its fluid limits are pushed to the upper extreme. Repetitive heating and cooling and pressure coax the plastic to envelope inserted materials to take on its irregularities.”
After the plastic and stone have unified, each table undergoes an intensive sanding and polishing process, using techniques Craig picked up working with local suppliers and experts.
He enjoys that part of the learning process as well: “This series connects me to different people and industries and gives me access to a whole community of experts and fabricators. The great thing about Detroit—and it’s helped my practice evolve, too—is that there are still all these fabricators and residual components of industry that are alive and well. Everything’s at my fingertips.”
And for someone so devoted to experimentation, that access is invaluable. Because for Craig, every new piece is a chance to push the limits just a bit more, and to add another dose of unexpected wonder into the everyday.