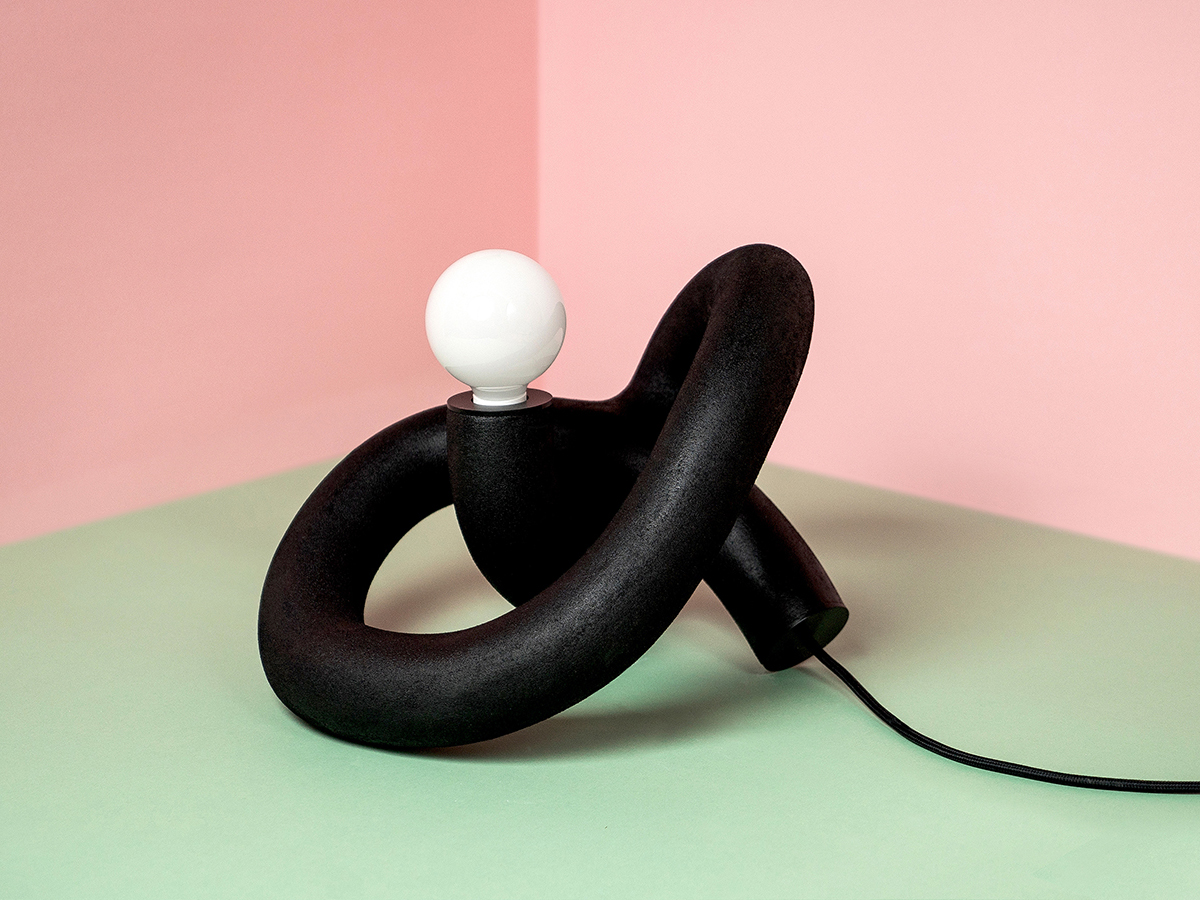
12.03.18
Up and Coming
A Furniture Collection in London Made From 3D Printing’s Leftovers
Years ago, when London-based designers Seongil Choi and Fabio Hendry met as students at the Royal College of Art, they were asked to make a stool — which, at the time, they had very little interest in doing. Yet by channeling their common backgrounds in industrial design and their interest in finding uses for low-value, abundant resources, they inadvertently developed an innovative process by which they have now made many, many a stool. Their signature furniture collection, called Hot Wire Extensions, is made by submerging nichrome wire (typically used for heating elements) into a bath of nylon powder leftover from 3D printers combined with pure silica sand. When the metal is heated, the surrounding granules sinter together and adhere to the armature to form a super-thick, powder-coated surface. The framework is manipulated by hand into woven, twisted, and sculptural shapes that lend an impromptu, sketch-like quality to the products.
Since graduating and setting up Studio Ilio back in 2015, the duo have worked on refining the process and developing a collection of furniture and lighting, which we’re featuring here today. Here, they talk us through their approach and their ambitions to apply the method to projects at a more architectural scale — bridges, public installations, and buildings.
Tell us a bit about where you met. When did you realize you had a similar or complementary approach?
We studied together at the Royal College of Art in London at the Master’s course of Design Products. In the first term, we had a brief to create a stool, which we both had little interest in. We had a common interest in how things are made and wanted to take this opportunity to research manufacturing processes. Having worked and studied in fields such as automobile design, bridge design and structural engineering prior to the MA, we both felt we wanted to implement as much as possible of this expertise into the design of products. Weirdly, we also realized that we both were intrigued by heat and its fascinating possibilities in combination with a material and a machine.
What drives the choices you make in your work — color, texture, form, process, material, environmental responsibility?
We are not very interested in color, per se, as a decorative element. We prefer if color is a result of the production process and as raw as possible. Unfortunately, the realities of having to sell our work often clashes with that. Similarly, we also think that elements such as texture, form, color and material are all interwoven characteristics of the manufacturing process and should be left as as natural as possible. This is the purest and most honest way to communicate an idea and should therefore also distinguish your intentions from other designers work. We believe that an original process will lead to a unique product. Environmental responsibility is standard for our practice, it’s the first question we try to answer with a new project. It is interesting for our generation of designers to amplify the ecological responsibilities of making, but it should never become a marketing tool.
Is your work driven more by hands-on experimentation or research?
There is definitely more hands-on experimentation happening at the studio than theoretical research. However, it is important to contextualize our actions, define the potentials and be aware of the consequences. In general, we start with a broad idea which is either based around a material or a production process. In order to open up some perspectives, we start with very intuitive, hands-on experiments. We start to build up a library of ideas and methods which are tested, analyzed and archived. We consider this part of the development process research, since it is the moment where you start to understand your process and your ingredients. From here, the fun starts, because we are familiar with the materials and the whole process becomes more pliable and versatile.
How exactly did you stumble upon such a unique and specific process?
We set out to develop a new type of process that could merge the gap between the sketch, the mockup, and the final product. We were drawn to the simple idea of using heat to, in some way, attract and transform a material from solid to fluid and back to solid. This led us to experiment with Nichrome-wire, which is easy to shape by hand, doesn’t require any tools, and can be heated to a couple of hundred degrees by simply putting an electrical current through it. We started to dream of objects that can be instantly and easily created, almost like making a drawing.
Do you prefer that sketch-like aesthetic or do you ever try to corral it into a more confined form?
Heat spreads in a very organic way, which leads to fluid and organic shapes. But we use both sketch-like and more confined languages, depending on the concept. The sketch-like objects demonstrate the freedom of shaping with the wire and the more minimal shapes highlights the soft and organic form. Naturally, where the wires intersect there is more heat so it gets thicker – creating a strong joint. We go through phases; sometimes we sympathize with the organic shapes and other times, we are more attracted by geometric, simplistic and archaic forms.
Is the process itself quite wild in terms of the outcome, or is it more controlled?
Anything that appears ‘wild’ is actually done in a considered and controlled manner. One of our main objectives was to create a viable industrial manufacturing process, even though if it was just for ourselves. The thickness and the joints can be estimated by temperature and time, so over the years, we have compiled detailed lists and charts of the variables within the process, which allow us to create identical objects.
What’s the weirdest thing you’ve ever made with this process?
The weirdest commission was a children’s bed frame for a television show on the BBC. It was a very unusual object and quite challenging in its size. The result was fun and we added some extra parts, such as shelves and clothing racks which can be attached with SLS printed joints.
Have you ever had any mishaps or mistakes that led you to learn a bit more about how it works?
Oh yes, of course! The whole project is built on learning from mistakes — there is often not much else to rely on.