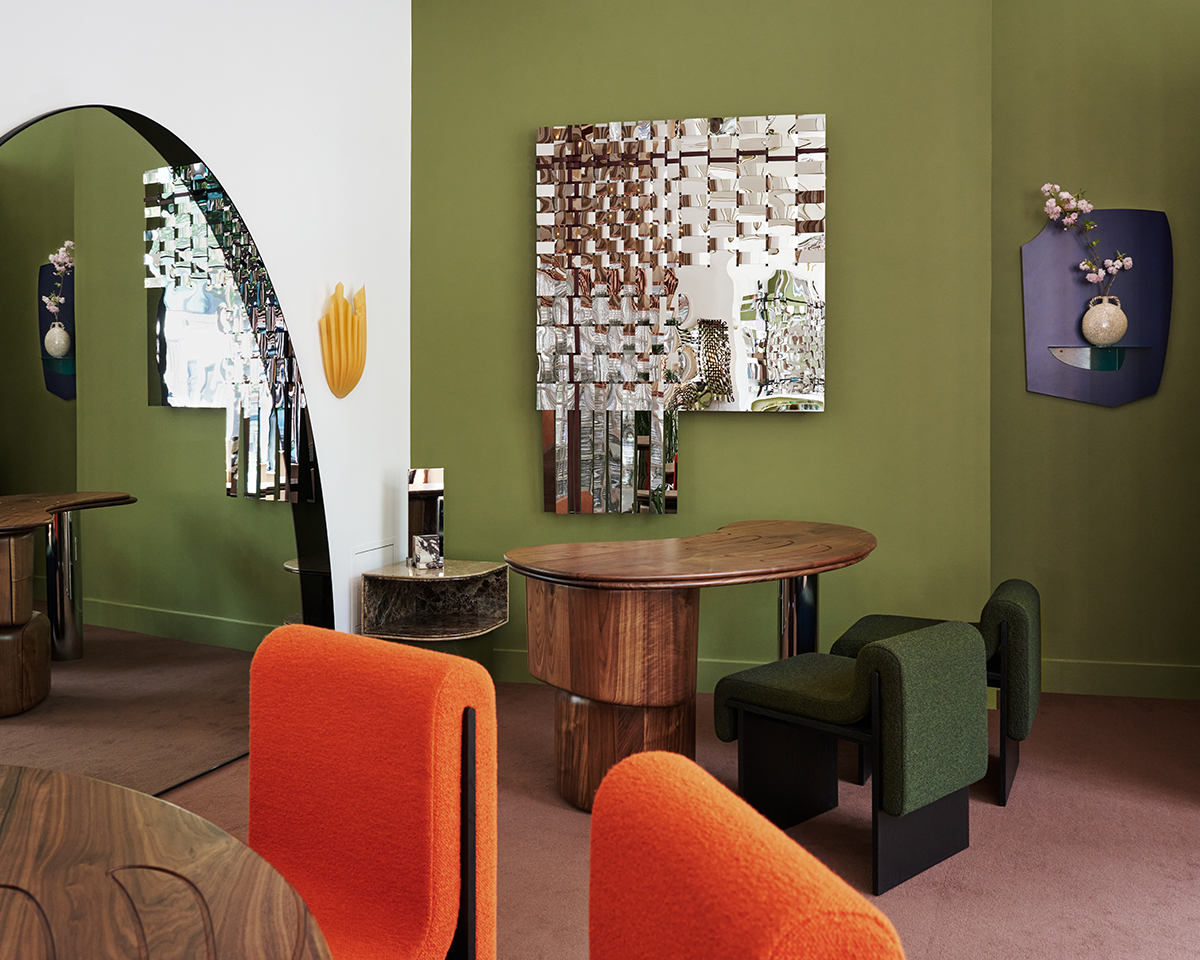
06.05.25
Excerpt: Exhibition
This Bower x Emily Mullin Showcase Was the Unexpectedly Tough — and Perfect — Exhibition New York Design Week Needed
Here is a list of things I do not particularly like: surfaces designed to look as if they were tattooed, ceramics bound by chains or ropes, almost anything with spikes. Part of the reason I don’t like these things is that, as a child of the ’90s, they often feel a little poser-y to me — like the designer thought that by using the signifiers of toughness that they could take a shortcut to actually being that thing. But you know what I do like? When designers use materials or processes that are often associated with something hard or edgy in an unexpected or weird or superfluous way. One tab I’ve had open on my computer for months is a listing for Paolo Piva’s Arcadia chairs for B&B Italia. The chairs are upholstered in black leather and the seat and back are joined by two chrome arcs. The arcs are weird; they should read like nose rings for the chair (another thing I don’t particularly care for), but to me they just seem effortlessly cool. I saw these in an art gallery in Stockholm in February and can’t get them out of my head five months later.
This was the exact feeling I got when looking at Bower’s new Woven collection of mirrors, which they debuted during New York’s month of design at the Mociun showroom. In each mirror, thin strips of leather are woven through a grid of mirror-polished stainless steel; a kind of Anni Albers for the post-punk era. They’re slightly hard to understand in pictures but mesmerizing in person, and they’re the result of absolutely painstaking work; once you start weaving a strip, you really cannot stop. (That Tammer Hijazi, a co-founder of Bower with Danny Giannella, is a massive Bottega Veneta fan is not lost on me, and I genuinely think fashion companies are dropping the ball if they don’t commission these for their stores or HQs!)
Also on view at the Mociun showroom were a series of glittering, cracked, or iridescent ceramics by Emily Mullin that achieve a kind toughness by way of the absolute berserk way in which they’re made. Do you know what the raku firing process actually involves? I didn’t before today. “Known for its dramatic results, raku involves removing ceramics from the kiln at peak temperature and placing them into containers filled with combustible materials — such as straw, newspaper, or sawdust. The intense heat ignites the materials instantly, and the container is sealed, creating a reduction environment that smokes the clay and activates the glazes. This fast and volatile process produces striking surface effects — iridescent glazes, metallic lustres, and intricate crazing patterns — and each firing yields unique, often unpredictable effects, making every piece a record of its own atmospheric conditions.” Take a tour through our favorite exhibition of the week below.