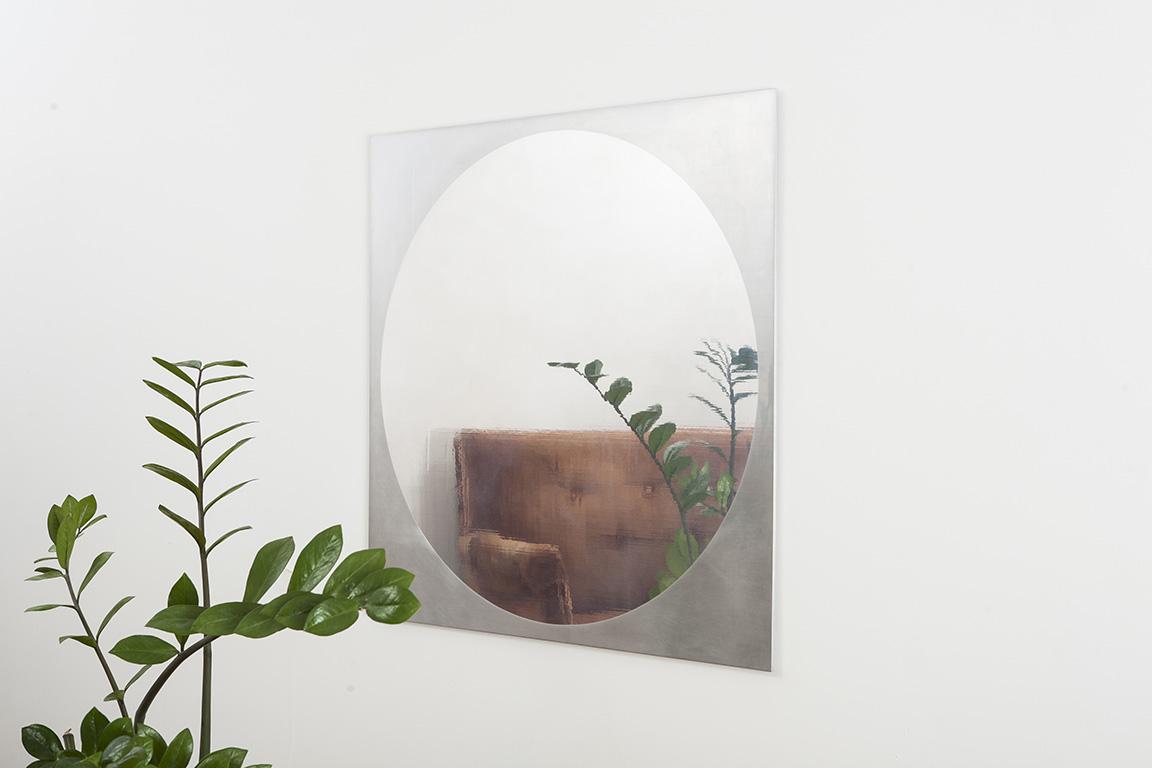
02.05.14
Sighted
Assembly’s 2x Aluminum Mirror
PHOTOGRAPHY BY MIKE GARTEN
As journalists, it’s basically our job to be professional busybodies, so there’s almost nothing that gives us a bigger thrill than when designers offer us a sneak peek at what they’re working on next. This week, those designers were the unfailingly prolific Pete Oyler and Nora Mattingly of Brooklyn-based Assembly, whose work we’ve featured extensively on the site. Their brand new piece is the 2x Aluminum Mirror, which is crafted from a solid sheet of 1/4-inch aluminum that’s been finished with two different techniques in order to create both reflective and opaque effects on the same surface. Says Oyler, “It’s part of a broader collection of work, to be released at ICFF in NYC this May, that bridges highly skilled hand and machine processes to explore extremes, subtleties, and possible outcomes within common materials.” Of course we decided to snoop around a little more and asked Oyler to tell us a bit more about it.
Can you tell me more about the collection of work you’ll be debuting in May? What are some of the other materials and processes you’re exploring?
For the past few months we’ve been really focusing on subtleties, extremes, and possible outcomes within singular materials. We developed the 2x Collection out of a want to highlight common materials and highly skilled hand and machine processes. From glass and pine to aluminum we’re taking common materials and applying both traditional and very experimental techniques to create utilitarian pieces that have a strong yet subtle presence.
My own background in design is pretty varied — I went to a traditional craft school, Penland, before attending RISD and I’ve always been very committed to the idea that the more technical knowledge one has about a material the more creative license one has a designer. While my own technical background is mainly in woodworking, I’ve made a big effort — driven mostly by sheer curiosity — to understand other media, processes, and methods. This collection we’re in process with speaks to almost a decade of being heavily immersed in conversations about craft, design, and technology.
Ultimately, I think all of the pieces we’re currently working on really celebrate risk and material integrity.
What are the two finishing techniques you used on the mirror?
The mirror is one solid sheet of aluminum, and the mirrored surface is achieved with a milling machine. There are very subtle gridded lines in the mirrored area that are remnants of the bit that was used to create the surface. The surrounding area is then brought to a satin finish by hand, with a template, and very carefully. Both of the processes employed illustrate the versatility and beauty of the material as well as creative and understated production methods.
When describing the mirror, you say, “The closer the subject is to the mirror, the clearer the reflection.” How do you achieve that effect?
The mirror finish is a result of milling. That milling process is visible in the final product, which means there is a certain almost wave-like effect in the mirrored area. When an object or person is close it is easier for our eyes to focus. From a distance, the mirror has a very painterly impact by virtue of its surface texture.