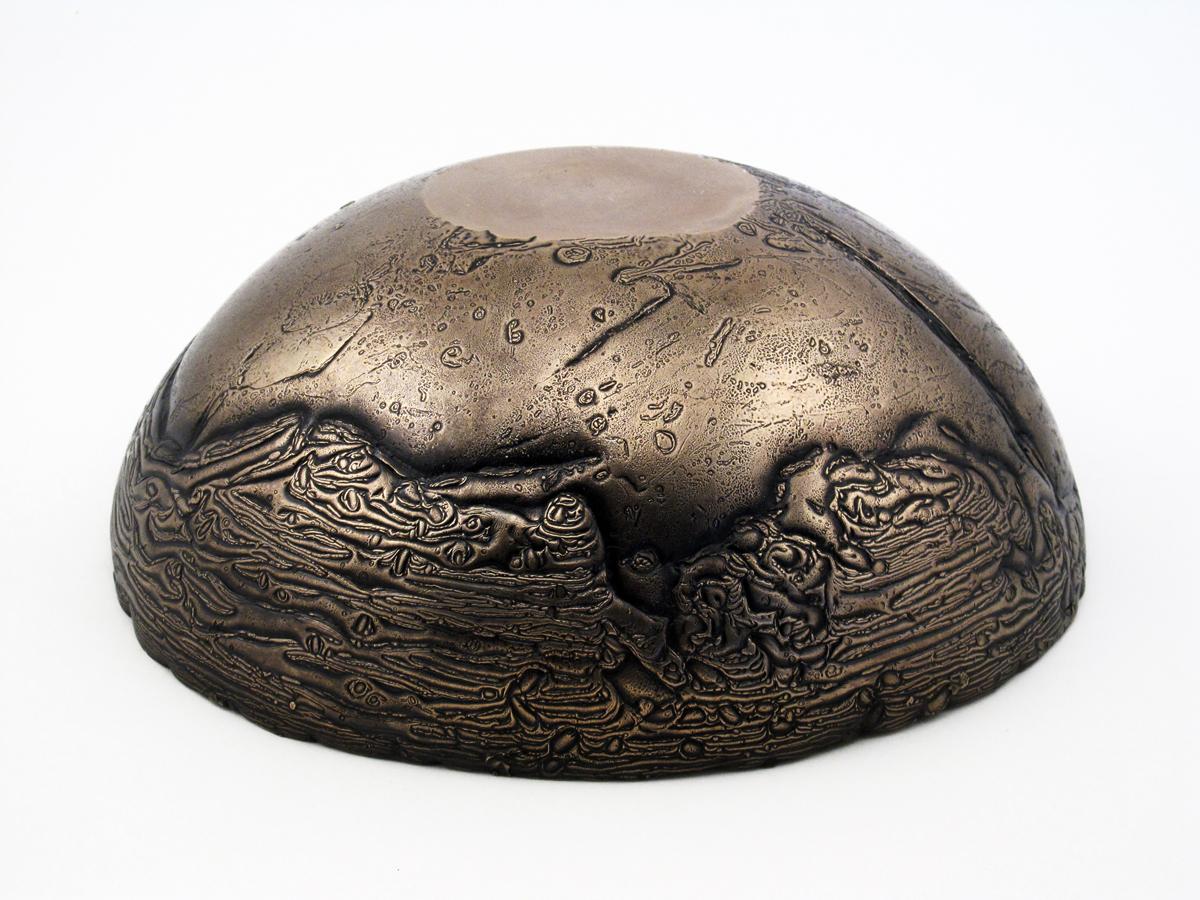
09.19.14
The Making of
Steven Haulenbeek’s Ice-Cast Bronze Collection
We’ve heard of something being a product of its environment, but never has that phrase rung so true as it does with the pieces in Steven Haulenbeek’s Ice-Cast Bronze series, on view this month at Chicago’s Casati Gallery, which were made largely in a trough of ice outside Haulenbeek’s studio window during last winter’s deep freeze. Haulenbeek — who knows from frigid winters, having grown up and studied sculpture in Michigan and lived in Chicago for the better part of his adult life — originally conceived the series back in 2011, when he was fooling around with pouring wax into frozen puddles on Chicago’s city streets. But this winter’s extreme conditions — while providing little but consternation for everyone else — gave Haulenbeek the opportunity to take the whole operation onto a much larger scale. We recently spoke with the Chicago-based designer to find out a little more about the origins and making of his new collection.
This particular project is extremely materials- and process-based. Is that how you usually work, or do you tend to come at things from a more conceptual point of view?
Coming from a sculpture background, I’ve always been very hands-on. I never start with a computer; often I don’t use a computer at all, which is why my shit is so out of date (laughs). I’m making sketches all the time but more often than not I’m sketching in real materials — which is how the Ice Cast Bronze pieces started. Even before there’s an idea for a design and before there’s a typology linked to it, I’m experimenting with materials and understanding what I can do with them and how I can apply that rather than drawing something and trying to get as close to that drawing as possible.
Did this project have its antecedents in anything you’ve done before?
The bronze thing is entirely new. It actually started with a relationship I had with a foundry. I used work at Holly Hunt, and my studio manager Angie West and I became very good friends. When we quit at almost the same time, she bought into this foundry called West Supply. All of a sudden I had a key and access to a foundry and could use all their stuff. So I started to hang around — a lot. I started to learn the processes, one being the lost wax process, which is a common casting process. Once I learned the process I began to understand where I could make a small intervention.
Now they’re in a really beautiful building, but the first foundry we were in was a train wreck — when it rained outside, it rained inside, it was freezing cold, and there was no heat. It was the dead of winter in 2011, and I was there at 3 or 4 in the morning messing around and it was freezing. I was working with hot wax, doing all these experiments, and for one of them, I took a cup of hot wax — which is at 300 degrees — and poured it into a frozen puddle. And it made that crazy, chaotic, raisin-y texture. That was the very beginning of it. It’s kind of nice that this process was partially created by the environment in Chicago.
Has the process changed much since those first experiments?
After I poured that first wax puck in the puddle, I started to experiment — I’d take a stainless steel Ikea bowl, freeze it, and pour wax into that. Then I’d freeze water around that bowl and see what happened when I did that. Then I started pouring directly into ice, and that’s what I’ve stuck with. The first real vessels we produced I would just go to Polar Ice places and I’d buy a 10-inch cubed block of ice. I’d carve a cavity using a saw and chisels, pour the wax into the cavity, fill it up to the top and leave it in there for one or two minutes. The outer quarter-inch of wax hardened against the ice but the center was still liquid that I could pour out, and it would leave me a wax vessel that was very easily recreated in bronze using the lost wax process.
The first pieces were smallish vessels — bowls, vases, etc. Then I went and bought myself an ice-cream freezer off of Craigslist, which allowed me to freeze my own blocks of ice. I started working with different shapes, longer forms, skinnier pieces. Then this past year afforded me the opportunity to work outdoors. My parents came to visit and randomly brought this steel trough that they’d gotten out of my grandfather’s garage. It was over five feet long, and maybe 18 inches wide and 8 inches deep. They were like, ‘Grandpa thought you might want to use for your art projects!’ They have no idea what I do. I put it on the back porch under the grill and it sat there for 6 months. When winter came, it started to fill up with water and froze so I took it to my studio and put it outside. Of course this past winter was the most brutal freezing cold winter ever, and each time it got cold I would crawl out the window, carve it, pour wax in, pull it out, fill it with water, and do it all over again. I started creating these wide flat tabletops, and my first two side tables, which I showed at Wanted Design in May. More recently I bought a mega-freezer, which is like 7 feet long and probably 30 inches deep. You could fit like 8 bodies in there. So I’m starting to freeze larger blocks of ice.
Do you have any further plans to refine the process?
There are guys in the area who carve ice, tacky ice sculptures like dolphins and shot luges. But they have the ability to make any size block of ice, and they have the ability to mill it. They can do very precise work to produce anything you want in ice. I’d like to have them create some blocks for me that I can pour into, which will allow me to work larger. But right now I’m designing for the set-up I have. It’s kind of a nice constraint — the size restriction in some way drives the aesthetic.
What else affects the look of these things besides the different cuts in the ice?
You would think that ice is just ice, but pouring into negative 10 degree ice is totally different than pouring into 20 degree ice. Warmer ice or cooler wax will create a wider ripple, and colder ice or hotter wax will produce these tiny little micro ripples. I’ve found the sweet spot within that, but it’s always interesting when you pop the wax out. You never know what it’s going to look like. And with the bowls I’ve found a way to texture the inside as well. Instead of pouring wax out I’m actually removing it one ladle at a time, which drops the level of the wax slowly and creates this ripple effect.
Have you thought about branching out beyond bronze?
I’m not opposed to other materials; I actually just got an ingot of pewter that I’d like to work with. I’ve also been thinking about doing these in plastic and cutting out the entire casting process. To that end, I’m trying to source a plastic that works like wax — something that’s pourable, viscose when hot, but then becomes solid when cools. That way I could do different colors, and it could be less expensive. But I do love the bronze; it’s soft, it patinas naturally, and it’s expensive so it justifies a higher price point. Plus it’s just a beautiful process.